-
- News
- Books
Featured Books
- smt007 Magazine
Latest Issues
Current IssueIPC APEX EXPO 2025: A Preview
It’s that time again. If you’re going to Anaheim for IPC APEX EXPO 2025, we’ll see you there. In the meantime, consider this issue of SMT007 Magazine to be your golden ticket to planning the show.
Technical Resources
Key industry organizations–all with knowledge sharing as a part of their mission–share their technical repositories in this issue of SMT007 Magazine. Where can you find information critical to your work? Odds are, right here.
The Path Ahead
What are you paying the most attention to as we enter 2025? Find out what we learned when we asked that question. Join us as we explore five main themes in the new year.
- Articles
- Columns
Search Console
- Links
- Media kit
||| MENU - smt007 Magazine
The Quest for Perfect Products
November 11, 2024 | Marcy LaRont, I-Connect007Estimated reading time: 7 minutes
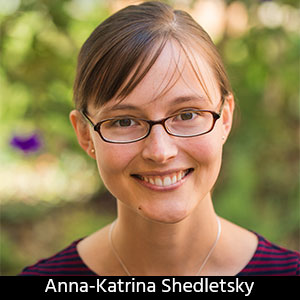
Anna-Katrina Shedletsky is a former Apple engineer who formed her own company, Instrumental, to address what she felt were frustrating and costly engineering problems and inefficiencies at Apple. She’s passionate about her quest to build perfect products faster than ever before.
In this interview, Anna shares her journey from creating innovative products like the Apple Watch to addressing the complexities of failure analysis in manufacturing. She also discusses an upcoming educational webinar she is hosting with Valentina Ratner, CEO of AllSpice.io, for engineering leaders in the manufacturing space. They look forward to providing “real talk” and value to their engineering colleagues.
Marcy LaRont: Anna, tell me about your background and why you formed Instrumental.
Anna-Katrina Shedletsky: I'm a mechanical engineer with two degrees from Stanford. Initially, I didn't know what I would do with those degrees, but I had this interest in “perfect products.” Intellectually, it’s such an interesting idea, and I had this naive assumption that Apple must make perfect products because they make a million iPhones a day. Even a 1% yield problem would be too many “bad” phones, so they must have the secret to perfect products. I was fortunate enough to be hired at Apple, and by day two, my bubble burst: Apple didn’t have perfect yields. No one in the industry does. I then spent the next six years at Apple learning why perfect products are really hard to make, how the pursuit of building perfect products is not cheap, and why that lack of perfection is so costly.
As a product design engineer, I worked on a handful of iPod programs. I also led the first-generation Apple Watch system product design. It came with a lot of innovation—and challenging problems. We were always grappling with this core challenge of how to find issues and fix them really quickly. The speed at which we could do that was dictated by the failure analysis engine.
At that time, a personal tragedy happened caused me to reevaluate how I was spending my time. I decided I wanted to work on something bigger than building beautiful watches. I started this company to help manufacturers try to build perfect products. I thought we could do that through technology. The innovation in that technology was the realization that the core engine driving both development and production is this failure analysis process.
Everyone must do failure analysis. In product development, we work to figure out what failures will happen, analyze and solve them, and establish corrective actions to carry into production. Failure analysis is the engine that enables process and yield improvement on production lines. Some call it root cause analysis, but it's the same thing. So, we set out to build technology that would augment—and eventually automate—failure analysis as much as possible. It would find problems that would allow the engineers to do the things that engineers do best, which is come up with creative solutions to problems. That's Instrumental in a nutshell.
LaRont: This is a very hot topic. Automation toward faster and better problem solving in manufacturing is greatly needed. Making product deadlines with higher technology demands is becoming more difficult.
Shedletsky: There's a lot of pressure from the C-suite to go faster because the length of time spent developing a product is the most expensive part of process. The faster you go, the cheaper it is to bring something to market.
LaRont: This enables you to cut down on your revisions.
Shedletsky: Yes. Essentially, you do a prototype build, then a second build, and then you try to ship. We're seeing this pressure and need across the industry, not just in consumer electronics. We see it in B2B electronics, networking, and rackables. We even see it in defense. There are different timescales in defense, but it's the same thing. They need to go faster.
Historically, there's been this idea that faster inevitably means poor quality, but I think that bubble has burst. It’s not a zero-sum slider anymore. There are ways to go faster with excellent quality; you don't have to trade off. We live in this amazing age where technology can help us do those things.
LaRont: All Spice.io was part of the Build Better 2024 conference, where you and I met. Tell me about the webinar with Valentina.
Shedletsky: Valentina and I are engineers who found the inefficiencies in engineering to be very painful and quit our jobs to try to solve these issues. For this webinar, scheduled for 11 a.m. PST/2 p.m. EST Wednesday, Nov. 13, we're reaching out to engineering leaders to talk about the things that really matter to them, and discuss their agitating pain points. We know that chief among their concerns is speed or time-to-market.
If that’s the priority, how do you find speed in your organization? One of the challenges for leaders is they don't know how to measure or even calculate the benefit of speed: “Here's how much an additional DOE (design of experiment) costs, not just in the cost from the factory to do the DOE, but also the head count, the delays, etc.” They don’t really know how to measure cost when the failure analysis takes six days instead of six hours.
As an engineering leader, you intuitively know it’s adding up and it’s expensive, but I think many leaders are really surprised at how big those numbers get and, in some cases, how quickly they get there.
LaRont: Will you be providing a basic algorithm to help companies do that?
Shedletsky: Yes, we will share three steps to boost productivity and achieve greater speed: discover where your inefficiencies are, know how to measure them, and know how to implement changes. It will help engineering leaders think about the tactical things they can do in their organizations, even if it’s just wrapping their arms around the inefficiencies they have and identifying the places where they could potentially go faster.
LaRont: It sounds like you are trying to effect a paradigm shift in how leaders in product manufacturing view their processes and process improvement.
Shedletsky: That’s right, but I think the most common hangup is how to measure between soft and hard ROI. Hard ROI is very easy; nobody has problems with that. You pull a person off the line, and get the headcount with its associated cost. But the problem is when you pull that person off the line, realize your headcount savings, and still ask, “Did I see a quality improvement? Did I get a speed improvement?” Are you now creating units that need to go through FAA, and will take three engineers multiple hours a week to process? The downstream impact of a one single hardware event is very large. Manufacturing is complicated, and changing one thing affects many things.
For engineering leaders who want to do valuable things and create speed in their organization, the good news is that small change can make it more efficient and have massive value across the organization. It is an opportunity for leaders to elevate themselves in their organizations. They can make a change in their area that directly impacts the P&L statement for the business. It is really exciting when engineering leaders realize they have the ability to change a top-line revenue number just by making a change within their part of the organization.
LaRont: How do Instrumental and AllSpice.io complement one another?
Shedletsky: AllSpice.io is a company focused on providing a technology solution that drives easier communication and collaboration between engineering teams in product development and manufacturing to positively affect quality and cycle time, and decrease revisions in product development. Instrumental’s solution utilizes technology to drive quality and speed through a faster and better way to conduct failure analysis. Both our companies target the interface between different engineering groups. Where we overlap is that Valentina and I have a vision to make it easier to get everyone working in the same direction. Our solutions are independent but complementary.
Our discussion in the webinar around these challenges will be valuable because we will share different perspectives, and one perspective may aligned well to a certain type of organization whereas another perspective will be good for someone else.
LaRont: Anna, is there anything else that you'd like to say about the webinar?
Shedletsky: It will be “real talk.” If you want to cut through the noise and actually have something you can take back to your own organizations and leverage that information, this webinar is for you.
LaRont: How can we register?
Shedletsky: You can register on the Instrumental website.
LaRont: Thank you, Anna. Good luck and thank you for hosting an educational webinar on such an important topic.
Suggested Items
25 Years of IPC APEX EXPO: Organizer Alicia Balonek Reflects on a Milestone
03/28/2025 | Alicia Balonek, IPCAs I celebrate my 25th work anniversary with IPC, I can’t help but reflect on my incredible journey. From its inception in 2000, IPC APEX EXPO has evolved into one of the most anticipated and dynamic events in the electronics industry, and I’m proud to have been a part of its growth every step of the way.
Target Condition: Designing vs. Inventing
03/27/2025 | Kelly Dack -- Column: Target ConditionAfter hearing me rave about IPC APEX EXPO for years, my boss, Chad Orebaugh, joined me at the show for the first time last year. We met at the registration counter, got our badges, and he said, “Okay, Kelly, impress me.”
Koh Young Presenting on Real-Time Process Optimization at SEMI Heartland 2025
03/25/2025 | Koh YoungKoh Young, the global leader in True 3D measurement-based inspection and metrology solutions, is pleased to announce that Luis Rivera, MES Team Leader at Koh Young America, will speak at SEMIEXPO Heartland 2025, taking place March 31 to April 2 in Indianapolis, Indiana at the Indiana Convention Center.
It’s Only Common Sense: The Danger of Overthinking
03/24/2025 | Dan Beaulieu -- Column: It's Only Common SenseWe’ve all had those moments when we find ourselves endlessly analyzing a decision, cycling through every possible outcome, and trying to anticipate every potential obstacle. It’s not just frustrating; it’s paralyzing. Overthinking is a timewaster, a progress-stopper, and a productivity killer. For many of us, it’s become a habit that keeps us from reaching our full potential.
Foxconn Unpacks Artificial Intelligence Progress At NVIDIA GTC
03/20/2025 | PRNewswireHon Hai Technology Group unveiled the first comprehensive look at its progress toward humanoid robotics, unrivalled infrastructure for the next generation NVIDIA GB300 NVL72 platform, and digital twins accelerating AI factories of the future, at the premier conference on artificial intelligence, GTC 2025.