One Partial HDI Technique: mSAP
November 5, 2024 | Andy Shaughnessy, Design007 MagazineEstimated reading time: 2 minutes
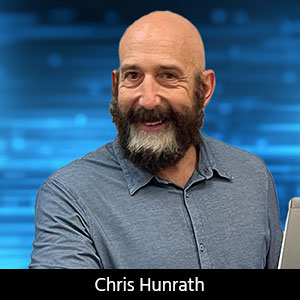
Partial HDI has shown itself to be very useful, allowing designers to escape route tight-pitch BGAs without moving to full HDI and the required sequential lamination. It’s almost the best of both worlds.
Chris Hunrath, vice president of technology at Insulectro, believes that mSAP just might be the trick for designers considering partial HDI. As Chris explains, the materials and equipment required for the mSAP process are easily available, and the process is well established. This could be a great option for designers working with BGAs that have a pitch of 0.5 mm or less.
Andy Shaughnessy: Chris, why would somebody choose to move to partial HDI? When does that process make sense, and when is mSAP the answer?
Chris Hunrath: It’s all about BGA pitch, microvia location, and circuit routing. I've not heard anyone call it partial HDI, but I like that expression because that explains it just right: the rest of that layer or the board might be more, let's say, conventional. But you neck down the traces to be able to do your fan-out. One of the things I've learned in the past couple of years from designers is that it's okay to make the trace narrower—you won’t degrade the signal integrity as long as that neck-down area is a short length. You can get your routing and still have some registration budget where you won't risk having defects like shorts and whatnot.
First, there’s a lot of what we call “head trash” about exactly what mSAP is. It's also really important to remember that pattern plating, which is done in North American PCB shops every day, is a semi-additive process. We're just taking it to the next level with mSAP. A lot of things are converging right now. You have the finer-pitched BGA packages that are being developed for multiple markets. That's another thing. It's one thing to have lots of room, but if the component is made for multiple markets, you're stuck with that pitch. You just can't go to a bigger pitch.
Another point is that exposure units keep getting better and more capable. If your board shop has a direct imaging machine, you likely already have that 25-micron capability. Some of the materials have come together as well, and we supply those materials.
To read this entire conversation, which appeared in the October 2024 issue of Design007 Magazine, click here.
Testimonial
"The I-Connect007 team is outstanding—kind, responsive, and a true marketing partner. Their design team created fresh, eye-catching ads, and their editorial support polished our content to let our brand shine. Thank you all! "
Sweeney Ng - CEE PCBSuggested Items
Polymatech Electronics Limited Announces Completion of PCB Manufacturing Facility in Europe
08/15/2025 | PR NewswirePolymatech Electronics Limited is thrilled to announce the successful commissioning of its state-of-the-art Printed Circuit Board (PCB) manufacturing facility in Estonia, Europe. This milestone represents a significant advancement in the company's strategic expansion across the European market.
Kaynes Circuits to Invest $570 Million in PCB Tech India’s Tamil Nadu State
08/07/2025 | I-Connect007 Editorial TeamKaynes Circuits India, a subsidiary of Kaynes Technology India, announced on Aug. 4 that it plans to invest roughly $570 million over the next six years in the southern state of Tamil Nadu, the Economic Times reported.
Inside the AI Hardware Boom: Servers, Substrates and Advanced Packaging
08/07/2025 | Edy Yu, Printed Circuit Information, China, and Marcy LaRont, I-Connect007AI is rewriting the hardware playbook, marrying complex software and algorithms to run and improve machine and equipment operations. Sorting through, managing, and utilizing massive amounts of data takes tremendous data storage and processing power. Enter the new generation of supercomputers and data servers. The data servers being built today are not your momma’s server, as they say.
UHDI Fundamentals: UHDI Technology and Industry 4.0
08/05/2025 | Anaya Vardya, American Standard CircuitsUltra high density interconnect (UHDI) technology is rapidly transforming how smart systems are designed and deployed in Industry 4.0. With its capacity to support highly miniaturized, high-performance, and densely packed electronics, UHDI is a critical enabler of the smart, connected, and automated industrial future. This article explores the synergy between UHDI and Industry 4.0 technologies, highlighting applications, benefits, and future directions.
Calumet Electronics Continues to Advance Domestic HDI Circuit Board and Organic Substrate Capability
07/25/2025 | Calumet ElectronicsCalumet Electronics Corporation, a leading American-made printed circuit board (PCB) manufacturer, today announces another major milestone in its ambitious program to bring advanced high-density interconnect (HDI) and high-density buildup (HDBU) capabilities online.