Unlocking Advanced Circuitry Through Liquid Metal Ink
October 31, 2024 | I-Connect007 Editorial TeamEstimated reading time: 1 minute
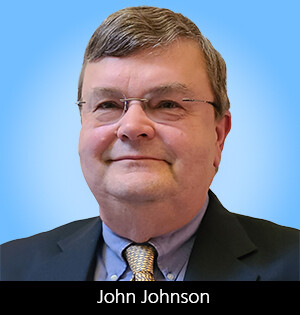
PCB UHDI technologist John Johnson of American Standard Circuits discusses the evolving landscape of electronics manufacturing and the critical role of innovation, specifically liquid metal ink technology, as an alternate process to traditional metallization in PCB fabrication to achieve ever finer features and tighter tolerances. The discussion highlights the benefits of reliability, efficiency, and yields as a tradeoff to any increased cost to run the process. As this technology becomes better understood and accepted, even sought out by customers and designers, John says there is a move toward mainstream incorporation.
Nolan Johnson: John, what is liquid metal ink technology?
John Johnson: It is a chemistry developed by LDQX (formerly Averatek) as part of its licensed solution for doing A-SAP™. Liquid Metal Ink (LMI™) is the heart of this process. The A-SAP process involves putting down a thin plating of electroless copper which forms the base of subsequent plate-ups for traces and so forth. You generate all your ultra-fine line circuitry with LMI. It is a non-aqueous substance that carries a palladium complex in solution. It can be coated through a dip method, a spray method, and other ways. At ASC, we use the dip method.
The beauty is that the LMI is key to the whole process. The palladium that's created is a very dense coating. It is a very unique approach. It touches atom to atom and is several atoms thick. It is semi-aqueous so it wets well, getting down into the small micro-topography that would be left behind if you had etched copper foil. The chemical bond to the copper foil is not significant, roughly only a 10% contribution to the total adhesion. Your adhesion comes from being able to coat on that micro-topography and plate it up with the right electroless. You get very good adhesion for a variety of different materials.
Nolan Johnson: If the chemical bond to copper is about a 10% contributor to adhesion, how much does the palladium affect adhesion?
John Johnson: With palladium there is no real chemical adhesion that takes place as the laminate is already cured, but it is important for adhesion in the subsequent processing.
To read this entire conversation, which appeared in the October 2024 issue of PCB007 Magazine, click here.
Testimonial
"We’re proud to call I-Connect007 a trusted partner. Their innovative approach and industry insight made our podcast collaboration a success by connecting us with the right audience and delivering real results."
Julia McCaffrey - NCAB GroupSuggested Items
Preventing Surface Prep Defects and Ensuring Reliability
06/10/2025 | Marcy LaRont, PCB007 MagazineIn printed circuit board (PCB) fabrication, surface preparation is a critical process that ensures strong adhesion, reliable plating, and long-term product performance. Without proper surface treatment, manufacturers may encounter defects such as delamination, poor solder mask adhesion, and plating failures. This article examines key surface preparation techniques, common defects resulting from improper processes, and real-world case studies that illustrate best practices.
The Chemical Connection: Surface Finishes for PCBs
03/31/2025 | Don Ball -- Column: The Chemical ConnectionWriting about surface finishes brings a feeling of nostalgia. You see, one of my first jobs in the industry was providing technical support for surface cleaning processes and finishes to enhance dry film adhesion to copper surfaces. I’d like to take this opportunity to revisit the basics, indulge in my nostalgia, and perhaps provide some insight into why we do things the way we do them in the here and now.
PCB007 Magazine: The Essential Guide to Surface Finishes—March 2025
03/17/2025 | I-Connect007 Editorial TeamIn the March 2025 issue of PCB007 Magazine, we go back to basics, recount a little history, and look forward to addressing the many challenges that high density, high frequency, adhesion, SI, and corrosion concerns for harsh environments bring to the fore.
Atotech to Participate at KPCA Show 2024
09/03/2024 | AtotechMKS’ Atotech will participate in this year’s KPCA Show 2024 in Incheon, held at Songdo Convensia from September 4-6, 2024.
Real Time with… THECA 2024: State of the Art Copper Adhesion
08/09/2024 | Real Time with... THECABruce Lee, MacDermid Alpha Electronics Solutions, joined Nolan Johnson following his paper presentation on the show's mainstage. Lee provided a detailed overview of the current state of adhesion promoters and discussed the interaction between mechanical adhesion, chemical adhesion, signal integrity, and substrate impacts.