Stringent High-speed Requirements Pose Technology Challenges
October 3, 2024 | Tarja Rapala and Joe Beers, iNEMIEstimated reading time: 2 minutes
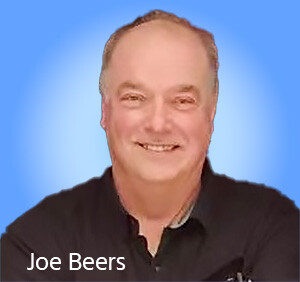
The ever-increasing demands on printed circuit boards to satisfy the needs of tomorrow’s products means that PCB manufacturers must continuously evolve and react to a wide variety of technological and market requirements such as: Functional density: Finer features, higher density, and increased layers; signal integrity: Higher frequencies, driven by higher data transfer speeds and increased data needs; material properties refinement: Must meet performance as well as environmental demands; Smart manufacturing: Automation, robotics, artificial intelligence, augmented and virtual reality, and machine learning are all part of the future PCB manufacturing floor; and time-to-market: Increased urgency to facilitate new design implementation, product introduction and qualification, quicker market differentiation, and survival.
To meet these stringent requirements, driven by expanding data needs and increasing transfer speeds, the electronics industry turns to high-speed PCBs and substrates. This article, based on the iNEMI Roadmap1, looks at some of the future requirements facing high-speed PCBs and substrates and discusses technical needs, gaps and solutions.
High-speed PCBs
The roadmap’s examination of high-speed PCBs focuses on solutions for high-speed digital applications such as high-performance computing in data centers. In this context, rapid edge rates, as encountered in signal rise time or fall time (whichever is less), define the signal as “high speed.” A rise or fall time of 1 ns implies a total signal bandwidth of 1 GHz or more, even with much lower switching speeds.
Technology evolution is driven by requirements to be:
- Faster: Interconnect speed will often be the limiting factor, particularly at the package level. Per-lane signaling speeds need to continually increase and that implies extra signal bandwidths. Issues such as losses and signal integrity will be critical.
- Smaller: Increased miniaturization in the core compute processing units leads to finer features and increased functionality and/or capacity on a given PCB, which leads to higher layer counts, as well as a reduction in all geometries.
- Hotter: Even with improvements in energy efficiency, heavier computing workloads from paradigms like machine learning and increased overall capacity will drive up power consumption. PCBs will have to accommodate higher power delivery and new approaches to thermal management, such as immersion cooling for data centers.
- Greener: PCB technology must become more sustainable, with the development of more energy-efficient manufacturing processes and with new materials and stackups supporting increased recycling and reuse.
- Cheaper: For infrastructure electronics, “cost” must include more than the bill of materials; it must focus on the full lifecycle. Improved reliability is a major objective to drive down lifetime costs.
To read the rest of this article, which appeared in the September 2024 issue of PCB007 Magazine, click here.
Suggested Items
Sypris Reports Q3 Results; Revenue Up 6.2%
11/19/2024 | Sypris Electronics LLCRevenue for the quarter increased 6.2% year-over-year, driven by a 13.6% increase for Sypris Electronics and a 0.7% increase for Sypris Technologies. Orders were up 6.5% for the quarter and 13.4% year-to-date, reflecting positive growth for both businesses.
India’s Wearable Device Market Dropped 20.7% in 3Q24
11/18/2024 | IDCAccording to International Data Corporation’s (IDC) India Monthly Wearable Device Tracker, India's wearable device market declined for the second consecutive quarter by 20.7% year-over-year (YoY) to 38 million units.
Compal Posts 3% QoQ Revenue Increase in 3Q24
11/12/2024 | Compal Electronics Inc.Compal Electronics announced its financial results for 3Q24. The consolidated revenue for 3Q24 reached NT$244.317 billion, marking a 3% QoQ increase.
Mycronic Releases Interim Report January-September 2024
10/24/2024 | MycronicOrder intake was basically flat in the third quarter, with decreases in Pattern Generators and High Flex compensated by increases in High Volume and Global Technologies. Net sales increased 40 percent, driven mainly by Pattern Generators, but with High Volume and Global Technologies also supporting the positive development.
Inside the New Facility at DIS
10/09/2024 | Marcy LaRont, PCB007 MagazineDIS has long been known as an equipment builder dedicated to PCB and assembly registration. Amidst a backdrop of increasing sales and expanding product lines, DIS has inaugurated a new facility and doubled its previous footprint. This move was aimed at enhancing operational efficiency and addressing space constraints that had plagued them for years, as well as allowing for the opportunity to expand their technology offering for their customers. In this candid conversation, Tony Faraci, owner and president of DIS, and Jesse Ziomek, DIS global sales director, delve into recent strategic advancements propelling the company forward.