PCB Surface Topography and Copper Balancing Under Large Form Factor BGAs
October 1, 2024 | Neil Hubble, Akrometrix and Gary A. Brist, Intel CorporationEstimated reading time: 1 minute
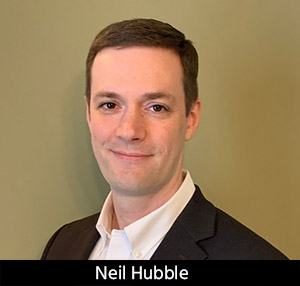
Editor’s Note: This paper was originally published in the Proceedings of IPC APEX EXPO 2024.
Background
As CPU and GPU packages grow larger and contain higher pin/ball counts, the importance of managing the printed circuit board (PCB) surface coplanarity for package assembly increases. The PCB surface coplanarity under a package is a product of both the global bow/twist of the PCB and the local surface topography under the package. In general, the surface topography is dependent the choice of material and layer stackup and the interaction between the innerlayer copper patterns and prepreg resin flow.
Advances in chiplet design and heterogeneous integration solutions in electronic packaging are enabling complex packages with increasing total die areas, resulting in the need for larger CPU and GPU packages1. Based on trends and advances in package integration, it is expected that future packages exceeding 100–120 mm on a package edge will become more common. This increases the challenge of the second-level interconnect (SLI) assembly processes when attaching the package to the PCB due to the combined coplanarity and topography variations of the PCB and package. These combined influences between the PCB and package are the key drivers of SLI defects such as solder bridging or solder joint opens during PCB assembly.2,3 Figure 1 is a graphical depiction of how the global PCB warpage or curvature under the package must be smaller for larger packages to achieve the same PCB coplanarity under the package.
Figure 1: PCB coplanarity under package.
The characterization of PCB coplanarity under the package footprint has been studied historically, including influences of assembly temperatures on dynamic PCB coplanarity as the PCB and package move together through the assembly reflow temperature profile.4,5,6 Other works have shown how the choice of PCB materials, fabrication process conditions, and design each impact global PCB bow/twist and warpage7.
To continue reading this article, which originally published in the September 2024 SMT007 Magazine, click here.
Suggested Items
Digital Twin Concept in Copper Electroplating Process Performance
07/11/2025 | Aga Franczak, Robrecht Belis, Elsyca N.V.PCB manufacturing involves transforming a design into a physical board while meeting specific requirements. Understanding these design specifications is crucial, as they directly impact the PCB's fabrication process, performance, and yield rate. One key design specification is copper thieving—the addition of “dummy” pads across the surface that are plated along with the features designed on the outer layers. The purpose of the process is to provide a uniform distribution of copper across the outer layers to make the plating current density and plating in the holes more uniform.
Trump Copper Tariffs Spark Concern
07/10/2025 | I-Connect007 Editorial TeamPresident Donald Trump stated on July 8 that he plans to impose a 50% tariff on copper imports, sparking concern in a global industry whose output is critical to electric vehicles, military hardware, semiconductors, and a wide range of consumer goods. According to Yahoo Finance, copper futures climbed over 2% following tariff confirmation.
Flexible Printed Circuit Board Market to Reach US$40.447 Billion by 2030
07/10/2025 | Globe NewswireThe flexible printed circuit board market will grow at a CAGR of 8.28% to be valued at US$40.447 billion in 2030 from US$27.17 billion in 2025.
TTM Technologies Prepares For the Future with the Acquisition of a Facility in Wisconsin and Land in Penang
07/10/2025 | Globe NewswireTTM Technologies, Inc., a leading global manufacturer of technology solutions including mission systems, radio frequency (RF) components and RF microwave/microelectronic assemblies, quick-turn and technologically advanced printed circuit boards (PCB), announced the acquisition of a 750,000-square-foot facility in Eau Claire, Wisconsin, as well as land rights for an additional future manufacturing site in Penang, Malaysia.
Schweizer Electronic: Annual General Meeting Approves All Proposed Resolutions with a Large Majority
07/10/2025 | Schweizer Electronic AGThe Annual General Meeting of Schweizer Electronic AG took place on June 27, 2025, at the company's headquarters in Schramberg.