Audits: A Critical Element of Process Control
September 3, 2024 | Randy Cherry, IPCEstimated reading time: 1 minute
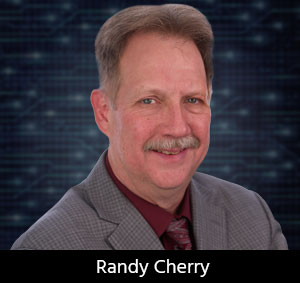
A formal audit always seems difficult to justify. Companies do not want the expense, and employees do not want the hassle. There is always a chance of failure, and management struggles to understand the benefits. If you or your company has had issues with auditing, hopefully, this article will help you feel a little more comfortable about the auditing process.
First, let’s discuss the internal process audit, which can help you avoid or eliminate many costly manufacturing problems, reduce scrap, increase yields, and directly improve your bottom line.
Process auditing can be simple and easy to maintain if you create a repeatable, impartial auditing process. Start with a Process Verification or Surveillance process audit. Create a basic yes/no checklist that covers each key manufacturing process within your facility. Another idea is to design a checklist covering all manufacturing processes from receiving to shipping and everything in between.
The Process Verification or Surveillance process audit is designed to be high-level. Unlike with a formal audit, objective evidence is not required. You are simply looking for gaps in the manufacturing process against your own internal procedures, standards, and work instructions. If your company operates by industry standards, add those to your checklist. It is best practice to perform Process Verification or Surveillance process audits once per quarter. As you collect and analyze data from the checklist, you can determine the most beneficial internal audit frequency moving forward. Let data drive the decision on audit frequency. Do not base it on opinions.
Going All the Way
Once you have determined your internal manufacturing processes and have met your goals for the Process Verification or Surveillance process audits, you may opt for the next step, which is to have a third-party auditor from an outside company perform a full manufacturing process audit to industry standards and your internal procedures and work instructions. The focus must be on the manufacturing processes, not your quality standards. Most companies have ISO certifications already in place that cover most quality concerns.
To read the entire article, which was originally published in the August 2024 issue of PCB007 Magazine, click here.
Suggested Items
SMTA Releases Final Batch of Training Resources Donated by Bob Willis
05/29/2025 | SMTAThe Surface Mount Technology Association (SMTA) announces the release of several more webinars, poster sets, and photo libraries to conclude a generous donation from renowned industry expert Bob Willis.
Driving Innovation: Traceability in PCB Production
05/29/2025 | Kurt Palmer -- Column: Driving InnovationTraceability across the entire printed circuit board production process is an increasingly important topic among established manufacturers and companies considering new PCB facilities. The reasons are apparent: Automatic loading of part programs, connection with MES systems and collection of production data, and compliance with Industry 4.0 requirements
ClassOne Technology, IBM Research Jointly Developing Non-NMP Solvent Processing for Semiconductor Manufacturing
05/26/2025 | ClassOne TechnologyClassOne Technology, a leading global provider of advanced electroplating and wet processing tools for microelectronics manufacturing, announced it has signed a joint development agreement with IBM Research focused on wet processing for advanced packaging.
KLA Invests in Operations in Wales with the Opening of a $138 Million R&D and Manufacturing Facility
05/23/2025 | PRNewswireKLA Corporation, a global leader in semiconductor process control and process-enabling technology, announced the opening of its new $138 million research and development (R&D) and manufacturing center in Newport, Wales, U.K., continuing the company's history of regional investment. SPTS, KLA's Wales-based product division, has been leading semiconductor equipment innovation in Wales since 1984, winning multiple Queen's Awards for excellence in R&D and export, and attracting strong technical talent to the region.
Pioneering Energy-Efficient AI with Innovative Ferroelectric Technology
05/22/2025 | FraunhoferAs artificial intelligence (AI) becomes increasingly integrated into sectors such as healthcare, autonomous vehicles and smart cities, traditional computing architectures face significant limitations in processing speed and energy efficiency