Candor: UHDI Under Development
December 21, 2022 | Nolan Johnson, I-Connect007Estimated reading time: 3 minutes
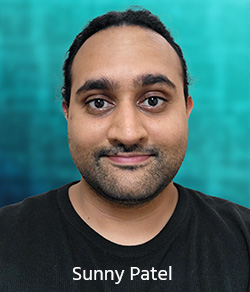
Candor Industries is a PCB fabricator investing in UHDI fabrication capabilities in Canada. To support advanced packaging, as well as the current pace of IC process shrinks, PCB fabrication capabilities must shrink to keep up. Sunny Patel, Candor’s technical sales manager, brings us up to speed on what Candor has learned in their journey to add UHDI. What we gain from this interview is that, while certainly not insignificant, the stretch to add UHDI may be not as far as one might think.
Nolan Johnson: Sunny, is Candor officially stepping into the realm of UHDI?
Sunny Patel: We’re starting to get there. The first dabbling in UHDI has been these direct on-chip boards that some of our customers are trying to do. Every layer seems sequentially drilled with 2-mil line and space, or 2-mil line with 1.5-mil spacing. We haven’t done a lot of it, but we have seen some demand for it.
Johnson: Where do you draw the line between UHDI and HDI? When does it become UHDI to you?
Patel: For us, UHDI is when it becomes more than sub-drilling and sequential blind vias; it’s a mixture of that, plus sub-3-mil lines/spaces, from my perspective. It becomes case-by-case specific on how to process these boards. I suppose that is the limitation of our equipment, but also our understanding of how things etch differently in that space. The basic tools that you have, the direct imaging, and the really tight registration of your layers are all important. But then you start getting into etch factor adjustments in different areas, like the horns or making sharper square pads, and extreme reduction of copper on the surface becomes very important.
Johnson: Do you need clean room facilities?
Patel: Most board shops use a clean room already or at least the ones I’ve seen; we all have a clean room. On the imaging side, that’s very important, but it’s more than that. It’s a whole new ball game. We’ve done the sequential blind vias, but how do we plate those areas but also limit the copper surface and make sure the etching is still perfect every time for every layer set? The processes are very involved now. You need someone who can look at the data. Based on experience, you know how things are going to etch in that sub-2-mil space and adjust here and there.
Johnson: Is there more custom tuning to get that ready to go?
Patel: Yes, and everyone in that space is experienced with semiconductor-level tolerances. There seems to be a big learning curve for those designers because they’re usually designing with that in mind. There seems to be a bit of a knowledge gap on learning how a circuit board factory works and the limitations of it all.
Johnson: Yes, the dimensions on the silicon 20 years ago weren’t much smaller than the dimensions we’re putting on the boards now. At that point for ICs, we were doing silicon in clean room environments and a great deal of standardization and process work and precision in that which doesn’t seem to have migrated over into the printed circuit board manufacturing industry until now. How close are we to needing to have a clean room environment throughout the facility?
Patel: I’m not entirely sure if we need a clean room for every system. But we need more control. Obviously, the imaging has always been a clean room setup, but the control of the plating and the control of the drilling becomes so much more critical. There doesn’t necessarily need to be a clean room throughout the whole department. For example, with a laser drill you need that vacuum system and the enclosed ventilation system in that kind of equipment whenever you’re doing the actual process.
With plating, it becomes more about chemistry control. The fluid dynamics must be fine-tuned to make sure that you’re even across the panel. That’s what people are transitioning toward, like the knife edge movement vs. the traditional rack movement of plating, enclosed vertical plating lines. So, the systems are becoming more controlled. I don’t know if the whole line must be in a clean room, but it has to be less open to the environment.
To read this entire conversation, which appeared in the November 2022 issue of PCB007 Magazine, click here.
Testimonial
"We’re proud to call I-Connect007 a trusted partner. Their innovative approach and industry insight made our podcast collaboration a success by connecting us with the right audience and delivering real results."
Julia McCaffrey - NCAB GroupSuggested Items
MKS Showcases Next-generation PCB Manufacturing Solutions at the Thailand Electronics Circuit Asia 2025
08/06/2025 | MKS Instruments, Inc.MKS Inc, a global provider of enabling technologies that transform our world, today announced its participation in Thailand Electronics Circuit Asia 2025 (THECA 2025), taking place August 20–22 at BITEC in Bangkok.
Point2 Technology, Foxconn Interconnect Technology Partner to Revolutionize AI Cluster Scalability with Terabit-Speed Interconnect
08/06/2025 | BUSINESS WIREPoint2 Technology, a leading provider of ultra-low-power, low-latency mixed-signal SoC solutions for multi-terabit interconnect, and Foxconn Interconnect Technology (FIT), a global leader in precision interconnect solutions, have signed a Memorandum of Understanding (MOU) to accelerate the commercialization of next-generation Active RF Cable (ARC) and Near Pluggable e-Tube (NPE) solutions.
Advancing Electrolytic Copper Plating for AI-driven Package Substrates
08/05/2025 | Dirk Ruess and Mustafa Oezkoek, MKS’ AtotechThe rise of artificial intelligence (AI) applications has become a pivotal force driving growth in the server industry. Its challenging requirements for high-frequency and high-density computing are leading to an increasing demand for development of advanced manufacturing methods of package substrates with finer features, higher hole densities, and denser interconnects. These requirements are essential for modern multilayer board (MLB) designs, which play a critical role in AI hardware. However, these intricate designs introduce considerable manufacturing complexities.
Statement from the Global Electronics Association on the July 2025 Tariff on Copper Foil and Electronics-Grade Copper Inputs
07/31/2025 | Global Electronics AssociationWe are disappointed by today’s decision to impose a 50% tariff on imported copper foil and other essential materials critical to electronics manufacturing in the United States.
Trouble in Your Tank: Metallizing Flexible Circuit Materials—Mitigating Deposit Stress
08/04/2025 | Michael Carano -- Column: Trouble in Your TankMetallizing materials, such as polyimide used for flexible circuitry and high-reliability multilayer printed wiring boards, provide a significant challenge for process engineers. Conventional electroless copper systems often require pre-treatments with hazardous chemicals or have a small process window to achieve uniform coverage without blistering. It all boils down to enhancing the adhesion of the thin film of electroless copper to these smooth surfaces.