Estimated reading time: 3 minutes
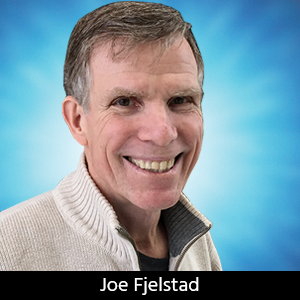
Flexible Thinking: Profitability—A Vital Design Requirement
Designers have, from the earliest days of the printed circuit industry, been under-appreciated. PCB designs were typically simple, single metal layer affairs, and design activities were considered a mundane (and even boring) task of “connecting the dots;” thus, they were given little respect.
Much has changed over the years, as integrated circuit technology has advanced, and data rates and processor speeds have climbed. Over recent years, I have found myself often saying that designers are arguably the most important people in the development of electronic products. The decisions they make will impact virtually every manufacturing step in the fabrication and assembly of electronics products. The designer’s role is so vital that, over the years, multiple touchstone guidelines have been added to the mix that seek to address myriad concerns that are all part of meeting the goal of producing the best possible products.
“Design for” Guidelines
The first order of concern for any design is that it simply meets the functional goals of the product. This can be accomplished in many ways, but beyond clearing the bar of “Does the product work?” there are many other litmus tests that are being more frequently applied to the evaluation of a completed design. These include design for manufacturing (DFM), design for assembly (DFA), design for testing (DFT), design for the environment (DFE), design for reliability (DFR), design for excellence (DFX), and there are doubtless other “design for” guidelines for other aspects that are deemed important to an individual types of products. All these guidelines provide important considerations relative to the product design in review. When applied, all of these “design for” guidelines combine to create products that can be made both reliably and profitably.
Designing for Profitability (DFP)
Good product design is arguably the cornerstone of every profitable product. Make a product that results in a loss or less than optimal return, and you are either headed for bankruptcy or irrelevance. It is possible to make unprofitable products as one climbs the learning curve or to gain or control market share (many governments subsidize products for this purpose). However, you must nevertheless offer the user something new and of perceived value even if the value is short-lived.
In this regard, it is important that designers work collaboratively with those who will be tasked with manufacturing their designs. Too often, designers work in isolation and do not have a full appreciation of the impact of the choices they make. The products they design are fabulously innovative, but if they cannot be built, and built profitably, what value is there in their effort?
Engage Others in the Design Process Early
How do we overcome this? Make sure all stakeholders involved in the manufacturing and testing of the product have input. Such in-put need not be tapped for every new design if the design is very similar to a past product design, but it does not hurt to have a check-list similar to that used by pilots before every flight. It may seem unnecessary, but an experienced pilot only needs to miss one item on the checklist to cause a potential disaster. “Design for” guidelines can help one to create such a checklist to ensure profitability. Finally, there is a need to make sure that the guidelines are followed. Societies have laws and rules for numerous reasons, but perhaps the most important is that they provide for the continuity of the societies themselves. (If not for traffic lights and stop signs, we would likely need to have either hospitals or cemeteries at every intersection.) Guidelines are different than laws, but the impact of not having them could be similarly troublesome. However, rather than a stringent set of dos and don’ts, al-low some discretion, depending on the product and its application. Advances in technology and innovation could be stifled if the de-signer is not allowed to explore the limits from time to time.
Summary
Designers are definitely “at the controls” at the beginning of every new product launch. Their decisions will impact everything that fol-lows their efforts, including the ultimate profitability of the final product. The use of established “design for” guidelines will serve them well in their work to ensure a smooth transition from concept to product and the future well-being of their company, client, or customer. As I have found myself saying with ever-greater frequency in recent years, we must all first do the right things, and then do those things right. It all begins with design.
This column originally appeared in the March 2020 issue of Design007 Magazine.
More Columns from Flexible Thinking
Flexible Thinking: The Key to a Successful Flex Circuit Design TransferFlexible Thinking: Flexible Circuit Technology—Looking Back and Forward
Flexible Thinking: Mind-tapping into January
Flexible Thinking: Another PCB Design Paradigm Shift in the Works
Flexible Thinking: Rules of Thumb—A Word to the Wise
Flexible Thinking: Musings on High Density Interconnections
Flexible Thinking: Integrated Passive Devices—Design Solutions With Many Benefits
Flexible Thinking: Mechatronics in a Flex World