-
- News
- Books
Featured Books
- smt007 Magazine
Latest Issues
Current IssueThe Rise of Data
Analytics is a given in this industry, but the threshold is changing. If you think you're too small to invest in analytics, you may need to reconsider. So how do you do analytics better? What are the new tools, and how do you get started?
Counterfeit Concerns
The distribution of counterfeit parts has become much more sophisticated in the past decade, and there's no reason to believe that trend is going to be stopping any time soon. What might crop up in the near future?
Solder Printing
In this issue, we turn a discerning eye to solder paste printing. As apertures shrink, and the requirement for multiple thicknesses of paste on the same board becomes more commonplace, consistently and accurately applying paste becomes ever more challenging.
- Articles
- Columns
Search Console
- Links
- Media kit
||| MENU - smt007 Magazine
Estimated reading time: 6 minutes
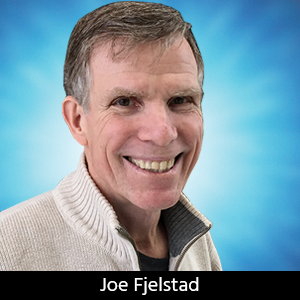
Flexible Thinking: Rules of Thumb: A Word to the Wise
In the early days of electronics manufacturing—especially with PCBs—there were no rules. Engineers, scientists, and technicians largely felt their way around in the dark, making things up as they went along. There was a great deal of innovation, guessing, and testing to make sure that early guidelines and estimates were correct by testing them. Still, they frequently made mistakes.
That said, they employed solid mechanical and electrical engineering practices, much like they do today. Over time, engineers have developed the “rules of thumb” in printed circuit board and flex circuit manufacturing. These are simplified guidelines based on the practical experiences of both individuals and the industry at large, rather than using strict and detailed calculations, and can help engineers and designers speed up the decision-making process, especially in complex scenarios. They are useful, but it's essential to know when to apply rules of thumb, which ones to prioritize, and when to rely on more precise calculations or formulas.
Where Rules of Thumb Work Best
Early phases of design: Rules of thumb are best applied in the early phases of the design and development process where they can help design and manufacturing engineers make quick assessments about board dimensions, component requirements and energy density limits, layer counts, and board materials. They can help the product developer or development team stay within budget by providing cost estimates and ballpark figures related to materials, fabrication, and assembly.
Prototyping: This has long been an important step in developing a new product and can often be sped up by employing rules of thumb. The purpose of the prototype is to establish the viability of the product and expose any intrinsic and/or unseen weaknesses in the design. It is a way to make and break things faster—a modern manufacturing mantra that won’t lead to “analysis to paralysis.”
Time constraints: Product developers have come to appreciate time, which is the most valuable commodity in life, whether that applies to products or people. When development timelines are tight, rules of thumb and guidelines can help expedite the process and reduce the need for extensive research.
An Overview and a Few Examples
Over time, the industry has developed different rules of thumb. Some were quite useful in their day but lost relevance with the fast pace of technology.
Capacity of current in traces: One rule of thumb with deep roots is related to the current-carrying capacity of traces, specifically that a conductor trace’s width should be roughly 1 mil (25 mm) for every amp of current draw anticipated. This rule harkens back to when 1-ounce (1.3 mil) copper was the de facto standard for foil. It is a relatively “safe” rule, but it should be modeled when putting design into practice. Similarly, there was a recommendation for some years that the designer maintain at least 3 mils (75 mm) of clearance between traces for basic applications to prevent electrical shorts and issues with manufacturing tolerances. This is, of course, a rule that is today seeing increased violations as HDI and UHDI with much finer circuit features become more common.
Plated through-holes and microvias: Plated through-hole vias were the first instantiation of a circuit feature not designed to receive a component pin. This followed the realization that a plated hole was a superior and much less costly solution to sticking a wire into a non-plated hole and making connection from side to side by soldering the ends of the wires to copper pads. Realizing that all holes are "a waste of space," designers and manufacturers had to compromise relative to the aspect ratio. For example, a 6-mil hole in an 062" thick board has an aspect ratio of roughly 10:1 and the same 6-mil hole size in a 0.120 mil has a 20:1 aspect ratio.
This was not easy in earlier times; however, using today's advanced plating chemistries, printed circuit boards with such features can be fabricated using build-up technologies and employing blind vias. They are increasingly being specified as a result. While not impossible with thicker boards to plate higher aspect ratios, employing plated through-vias in designs is not always desirable because they are necessarily larger. However, it is quite possible to design build-up boards with blind vias having aspect ratios that are square (1:1) or even “over square” (1:2) when using thin dielectric materials. This translates to a 2-mil hole in a 2-mil dielectric in the first case and a 4-mil hole in the same 2-mil dielectric in the second case. Such small vias can be helpful, or even crucial, in meeting routing density requirements, such as those increasingly needed for the layers of redistribution wiring required for today's high pin count components.
There have been several rules of thumb and guidelines devised for flex circuit manufacturing over the years as it matured from art to science:
Using copper in design: This has been a commonly practiced rule among flex circuit designers (Figure 1) because maintaining the extra copper helps to enhance the dimensional stability of the circuit. Designing with a bias for copper is a practice particularly well-suited to single-layer flex circuit designs. Double-sided application is possible, and it can help in the manufacture of multilayer circuits by maintaining dimensional control (Figure 2).
Staggered layer lengths: Rules of thumb have been applied in flex circuit manufacturing to create staggered layer lengths to ease the flexing multilayer and rigid-flex designs. The technique is accomplished by slightly adding to the length of each successive flex layer, moving away from the bend radius. A common and historical rule of thumb is to add length equal to roughly 1.5 times the individual layer thickness, but the value can vary based on the tightness of the bend and the number of layers. However, the objective is to prevent buckling of the center of bend layers (Figure 3).
A Word to the Wise
Rules of thumb are arguably handy to use in the early design process, but they need to be used with some caution:
Some rules may oversimplify complex interactions. In PCB design, this can include thorny challenges such as heat dissipation or impedance control design calculations.
Remember the era in which a rule of thumb was developed. Those created for older manufacturing technologies, processes, and practices may be irrelevant in more modern processes or materials.
Avoid assuming that rules of thumb are unaffected by variations in materials and processes used. They need to be carefully matched to the current design.
Summary
Rules of thumb can help guide and speed designers and engineers through initial decisions in the design process. However, traditional engineering practices and formulae remain highly important, even indispensable, as they provide the precision needed for final designs. Rules of thumb can simplify the myriad complex relationships that exist in circuit design and manufacturing, but tested and proven formulae derived from years of manufacturing practice that tacitly validate rules should be supported with empirical data when precision is critical and failure is not an option.
Using rules of thumb in PCB and flex circuit manufacturing can also enhance efficiency and decision-making, but they should be employed judiciously. Balancing these guidelines with detailed calculations and a clear understanding of the specific requirements of a project will lead to better designs and more successful outcomes. Always challenge assumptions and seek to validate decisions with data to separate myths from reality and ensure the ultimate reliability of the product. Above all, enjoy the process.
References
1. Flexible Circuit Technology, 4th Edition by Joe Fjelstad.
This column originally appeared in the November 2024 issue of Design007 Magazine.
More Columns from Flexible Thinking
Flexible Thinking: Musings on High Density InterconnectionsFlexible Thinking: Integrated Passive Devices—Design Solutions With Many Benefits
Flexible Thinking: Mechatronics in a Flex World
Flexible Thinking: PCB Designers Still Wanted
Flexible Thinking: Embedded Design—A Term With Multiple Meanings
Flexible Thinking: What Matters When Designing Next-generation Products?
Flexible Thinking: The Simplest Way Is the Best Way
Flexible Thinking: Unlocking the Key to Rigid-flex Design Success