-
- News
- Books
Featured Books
- smt007 Magazine
Latest Issues
Current IssueSupply Chain Strategies
A successful brand is built on strong customer relationships—anchored by a well-orchestrated supply chain at its core. This month, we look at how managing your supply chain directly influences customer perception.
What's Your Sweet Spot?
Are you in a niche that’s growing or shrinking? Is it time to reassess and refocus? We spotlight companies thriving by redefining or reinforcing their niche. What are their insights?
Moving Forward With Confidence
In this issue, we focus on sales and quoting, workforce training, new IPC leadership in the U.S. and Canada, the effects of tariffs, CFX standards, and much more—all designed to provide perspective as you move through the cloud bank of today's shifting economic market.
- Articles
- Columns
- Links
- Media kit
||| MENU - smt007 Magazine
Estimated reading time: 6 minutes
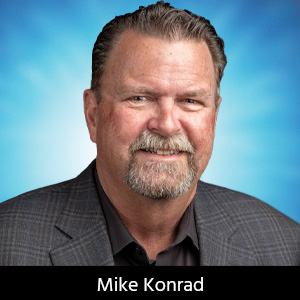
The Knowledge Base: Mastering the Art of Reworking Circuit Assemblies
In the dynamic realm of electronics manufacturing, the need for reworking circuit assemblies is an inevitable reality. Whether it's correcting defects, upgrading components, or adapting to design changes, the process of rework plays a crucial role in ensuring the functionality and reliability of electronic devices. In this column, we'll delve into the challenges, best practices, types, and reasons for reworking circuit assemblies, and shed light on the intricate world of electronic assembly modification.
Challenges of Reworking Circuit Assemblies
Reworking circuit assemblies presents a unique set of challenges that demand precision, expertise, and careful consideration. One of the primary challenges is the risk of damaging delicate components during the rework process. Soldering and desoldering components can expose them to excessive heat, potentially compromising their functionality or longevity.
Another challenge is the potential for introducing new defects during the rework process. Misalignments, solder bridges, or inadequate heat control can lead to unintended consequences and cause more harm than good. Moreover, as electronic devices become more compact and densely populated with components, navigating the intricate pathways of modern circuit boards requires a steady hand and keen attention to detail.
Best Practices for Reworking Circuit Assemblies
To overcome the challenges associated with reworking circuit assemblies, it’s essential to adhere to best practices. First, a comprehensive understanding of the specific assembly and its components is crucial. This includes knowledge of materials, thermal profiles, and the potential impact of rework on adjacent components.
Investing in high-quality tools and equipment is equally important. Precision soldering stations, hot air rework systems, and specialized tools for component removal contribute to successfully executing rework tasks. Additionally, utilizing soldering techniques such as drag soldering, hot tweezers, and vacuum desoldering can enhance accuracy and minimize the risk of damage.
Temperature control is a critical factor in rework success. Monitoring and controlling the temperature during soldering and de-soldering processes helps prevent thermal stress on components and the circuit board. This is particularly important when dealing with sensitive components such as microprocessors and integrated circuits.
Thorough documentation of the rework process is often overlooked but can be a lifesaver in troubleshooting and quality control. Detailed records of replaced components, soldering temperatures, and any modifications contribute to traceability and aid in future diagnostics.
Types of Rework
Reworking circuit assemblies can take various forms, depending on the nature of the modifications required. Here are some common types of rework:
- Component replacement: This involves the removal and replacement of faulty or outdated components, such as resistors, capacitors, or integrated circuits.
- Solder joint repair: Repairing solder joints with defects, such as solder bridges, cold joints, or insufficient solder, is a common form of rework. This ensures proper electrical connections and reliability.
- Modification and upgrades: Circuit designs may evolve due to changes in specifications or the introduction of new technologies. Reworking allows for modifications and upgrades to keep pace with advancements.
- Quality improvement: Rework is sometimes performed to enhance the overall quality of the circuit assembly. This can involve reinforcing weak connections, improving thermal management, or implementing design changes to address reliability issues.
Reasons for Rework
Understanding the motivations behind reworking circuit assemblies is crucial for both manufacturers and engineers. Several factors contribute to the need for rework:
- Design changes: As product designs evolve or specifications are updated, rework becomes necessary to incorporate these changes into existing circuit assemblies.
- Defects and failures: Manufacturing defects or failures identified during testing and quality control may require rework to rectify issues and ensure the final product meets quality standards.
- Component availability: Changes in component availability or the introduction of newer, more efficient components may prompt rework to improve the overall performance of the assembly.
- Customer feedback: Feedback from end-users or customers can highlight areas for improvement. Rework allows manufacturers to address issues and enhance the user experience.
- Cost reduction: Rework can be driven by the need to reduce manufacturing costs. For example, it could mean replacing a costly component with a more affordable alternative without compromising performance.
Hand Soldering
In the realm of reworking circuit assemblies, the application of industry hand soldering standards is paramount. These standards provide a comprehensive framework for ensuring precision, reliability, and consistency in manual soldering processes. Adherence to these standards not only enhances the quality of rework but also contributes to the long-term durability and performance of electronic devices.
1. IPC-A-610, Acceptability of Electronic Assemblies
IPC-A-610 is widely regarded as the industry standard for the acceptability of electronic assemblies. This comprehensive document defines the criteria for soldering, component placement, and other aspects of electronic assemblies, including those subjected to rework.
When it comes to hand soldering, IPC-A-610 specifies the acceptable criteria for various solder joints, ensuring that they meet the required quality standards. This standard classifies solder joints into different classes based on their application, with Class 3 being the highest standard for high-performance electronic products, and Class 1 being suitable for general-purpose electronics.
2. IPC-J-STD-001, Requirements for Soldered Electrical and Electronic Assemblies
Developed by IPC in conjunction with the Electronic Industries Alliance (EIA), J-STD-001 is another crucial standard focusing specifically on the requirements for soldered electrical and electronic assemblies. This standard provides detailed requirements for soldering processes, materials, and inspection criteria.
J-STD-001 emphasizes the importance of proper training and certification for soldering operators. It defines the skills and knowledge necessary for individuals involved in hand soldering processes, ensuring they possess the expertise required to effectively perform rework tasks.
3. ESD (Electrostatic discharge) control
While not solely focused on hand soldering, ESD control is a critical aspect of electronics assembly, including rework processes. Industry standards, such as ANSI/ESD S20.20, provide guidelines for establishing an ESD control program. Proper ESD control is essential during hand soldering to prevent damage to sensitive electronic components, which are prevalent in modern circuit assemblies.
Best Practices Derived from Standards
Incorporating the principles outlined in these standards into the rework process significantly contributes to the success of hand soldering. Some key best practices derived from these standards include:
1. Training and certification
- Ensure that personnel performing hand soldering tasks are adequately trained and certified according to industry standards
- Regularly update training programs to align with the latest revisions of soldering standards
2. Process control
- Establish and maintain control over soldering processes, including temperature profiles, soldering iron calibration, and equipment maintenance
- Monitor and document soldering parameters to ensure consistency and traceability
3. Inspection and quality control
- Implement thorough inspection processes based on the criteria outlined in IPC standards
- Conduct regular audits to verify compliance with soldering standards and identify areas for improvement
4. ESD mitigation
- Integrate ESD control measures into the rework environment to prevent electrostatic discharge-related damage
- Use ESD-safe tools, workstations, and personal protective equipment to safeguard sensitive electronic components
In the ever-evolving landscape of electronics manufacturing and rework, adherence to industry hand soldering standards is the linchpin for achieving excellence. These standards not only set the bar for quality but also contribute to the overall reliability and performance of electronic assemblies. By embracing the principles outlined in IPC-A-610, IPC-J-STD-001, and related standards, manufacturers and engineers can elevate the precision and reliability of hand soldering in the pursuit of excellence in electronic assembly and rework.
ConclusionReworking circuit assemblies is a complex yet essential aspect of electronics manufacturing. The challenges demand a combination of expertise, precision tools, and adherence to best practices. With an understanding of the types of rework and the reasons behind them, manufacturers and engineers can navigate this intricate landscape, ensuring the reliability and quality of electronic devices.
This column originally appeared in the January 2024 issue of SMT007 Magazine.
More Columns from The Knowledge Base
The Knowledge Base: Cultivating Your Brand in the Age of ConnectionThe Knowledge Base: A Conference for Cleaning and Coating of Mission-critical Electronics
The Knowledge Base: Building the Workforce of Tomorrow With EMAC
The Knowledge Base: Beyond the Badge—Why Membership Matters More Than Ever
The Knowledge Base: Unlocking the Invisible—The Critical Role of X-ray Technology
The Knowledge Base: At the Forefront of Electronics Manufacturing
The Knowledge Base: Challenges and Considerations of Harsh Environments
The Knowledge Base: My 2025 Industry Wish List