-
- News
- Books
Featured Books
- smt007 Magazine
Latest Issues
Current IssueSupply Chain Strategies
A successful brand is built on strong customer relationships—anchored by a well-orchestrated supply chain at its core. This month, we look at how managing your supply chain directly influences customer perception.
What's Your Sweet Spot?
Are you in a niche that’s growing or shrinking? Is it time to reassess and refocus? We spotlight companies thriving by redefining or reinforcing their niche. What are their insights?
Moving Forward With Confidence
In this issue, we focus on sales and quoting, workforce training, new IPC leadership in the U.S. and Canada, the effects of tariffs, CFX standards, and much more—all designed to provide perspective as you move through the cloud bank of today's shifting economic market.
- Articles
- Columns
- Links
- Media kit
||| MENU - smt007 Magazine
Estimated reading time: 4 minutes
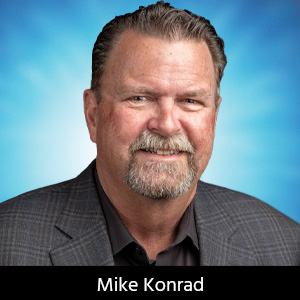
The Knowledge Base: Building Reliable Electronics for Harsh Environments
Editor’s note: Welcome to our new columnist, Mike Konrad, vice president of communications for SMTA. These monthly columns will feature conversations with industry experts and leaders across the electronics manufacturing spectrum. Over the years, Mike has often been asked about how to build reliable electronics in harsh environments. In this first column, he has compiled those queries into a question-and-answer format.
The explosion of Internet of Things (IoT),?electric vehicles (EV), wearables, medical devices, and other applications have presented substantial challenges for electronics manufacturers. Chances are, anyone who currently owns an electric vehicle is keenly aware of some of these challenges. It has been widely reported that up to 30% of public charging stations are inoperative. This fact is also known to the U.S. government, which is funding the expansion of high-speed charging stations through the CHIPS Act—with a caveat that the reliability of publicly funded high-speed charging stations must be greater than 90%.
With the SMTA Electronics in Harsh Environments Conference scheduled for May 23–25 in Amsterdam, I thought this would be a good opportunity to talk about the challenges and risks associated with building reliable electronics for use in harsh environments. I will also deliver a keynote address at the conference entitled, “The Remarkable Return of Post-Reflow Cleaning as a Mainstream Process to Improve Reliability.”
What makes harsh environments challenging for electronics?
There are several challenges associated with electronics in harsh environments. These challenges include extreme temperatures and temperature cycles, shock and vibration, electrostatic discharge (ESD), electromagnetic interference (EMI), and moisture, perhaps one of the least understood challenges.
What are the challenges and mitigation strategies regarding moisture?
Moisture on its own is not particularly harmful. The real issue is electrochemical migration (ECM). Moisture serves as a catalyst for ECM.
What is ECM?
ECM (electrochemical migration) is the dissolution and movement of metal?ions?in the presence of electric potential, which results in the growth of?conductive dendritic?structures between cathodes and anodes. This results in electrical shorts. The process is most observed in?printed circuit boards?where it may significantly decrease the insulation between conductors.
How does moisture serve as a catalyst for ECM?
There are three basic “ingredients” of ECM: electrical bias, conductive residues, and moisture. The main factor facilitating ECM is humidity (moisture). Usually the process involves several stages: water adsorption, anode metal dissolution, ion accumulation, ion migration to the cathode, and dendritic growth.
While ECM is not a new phenomenon, it’s occurrence is at historically high levels.
What is driving the historically high levels of ECM?
While there are several factors influencing the rising levels of ECM, the two primary factors are widespread adoption of no-clean fluxes and miniaturization. When no-clean fluxes were first introduced in the early 1990s, circuit assemblies were vastly different than they are today. Modern circuit assemblies and components are considerably smaller than any time in history. Previously, through-hole components were larger and placed farther apart. Larger spacings between cathodes and anodes provide a higher degree of residue tolerance. Modern circuit assembly designs have all but eliminated the spacing between conductors, reducing an assembly’s tolerance for residues.
The combination of a higher density of residues combined with smaller spacing between conductors has increased the propensity for ECM.
Isn’t it true that no-clean fluxes are residue-free?
All fluxes, including no-clean, leave behind residues. It is accurate to describe the residues from no-clean fluxes as both invisible and relatively benign. The primary issue at hand is not the residues left on an assembly from the no-clean flux, rather it is the totality of all process residues left behind on the assembly after reflow. Formerly, before the introduction of no-clean fluxes, virtually all circuit assemblies were cleaned after the soldering process. Not only did the cleaning process remove the flux residues, it also removed all process residues.
What other residues besides flux are left on the assembly?
Residues from board fabrication and component fabrication, as well as process and human residues, combine with flux residues to create a problematic totality of ECM-causing residues.
One should consider that when the industry stopped removing flux residues via a post-reflow cleaning process, it also stopped removing all residues. I frequently remind assemblers that we should not refer to residue removal as a “defluxing process” and more accurately rename it a “cleaning process,” because flux is only one residue species present on an assembly. It is the totality of residue species that, when combined with an electrical bias and moisture, creates an ECM potential.
You stated moisture is an ECM catalyst. If we simply apply conformal coating to the assemblies, won’t that prevent moisture-induced ECM?
While that is a widely held view, the fact is, conformal coating does not prevent moisture intrusion.
All conformal coatings are permeable. While they effectively prevent large volumes of fluid from contacting the assembly, they do allow small amounts of moisture to permeate through the coating. While conformal coating can delay an ECM event, it does not prevent it.
Another factor to consider is conformal coating adhesion. All conformal coating manufacturers recommend cleaning prior to coating. Coating over uncleaned surfaces may result in the delamination of the conformal coating.
Do you recommend assemblers move away from the use of no-clean fluxes?
Absolutely not. The fact is, no-clean fluxes and pastes are by far the most popular flux types used today. The sheer popularity of no-clean flux has created an environment whereby it is the most highly engineered and supported flux type within our industry. My recommendation is to continue using no-clean flux and identify and clean what assemblies need to be cleaned based on the cost of failure, the assembly’s tolerance for residues, and the expected reliability requirements.
This column originally appears in the May 2023 issue of SMT007 Magazine.
More Columns from The Knowledge Base
The Knowledge Base: Cultivating Your Brand in the Age of ConnectionThe Knowledge Base: A Conference for Cleaning and Coating of Mission-critical Electronics
The Knowledge Base: Building the Workforce of Tomorrow With EMAC
The Knowledge Base: Beyond the Badge—Why Membership Matters More Than Ever
The Knowledge Base: Unlocking the Invisible—The Critical Role of X-ray Technology
The Knowledge Base: At the Forefront of Electronics Manufacturing
The Knowledge Base: Challenges and Considerations of Harsh Environments
The Knowledge Base: My 2025 Industry Wish List