-
-
News
News Highlights
- Books
Featured Books
- smt007 Magazine
Latest Issues
Current IssueSpotlight on India
We invite you on a virtual tour of India’s thriving ecosystem, guided by the Global Electronics Association’s India office staff, who share their insights into the region’s growth and opportunities.
Supply Chain Strategies
A successful brand is built on strong customer relationships—anchored by a well-orchestrated supply chain at its core. This month, we look at how managing your supply chain directly influences customer perception.
What's Your Sweet Spot?
Are you in a niche that’s growing or shrinking? Is it time to reassess and refocus? We spotlight companies thriving by redefining or reinforcing their niche. What are their insights?
- Articles
- Columns
- Links
- Media kit
||| MENU - smt007 Magazine
Estimated reading time: 4 minutes
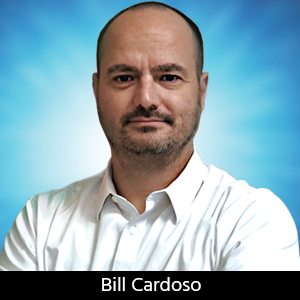
X-Rayted Files: My Favorite BGA Assembly Ever, Part 3
While the novelty may have worn off, let’s take one last look at my favorite BGA image. In part 2, we discussed issues of coplanarity, shorts and head-in-pillow. Now we will review the other common BGA assembly issues, illustrated so well in Figure 1. Whether or not you are fascinated by this, maintaining awareness of these common failure modes of BGAs, and inspecting for them throughout your process, will increase yield, reduce rework and scrap, and result in higher quality, more reliable products.
Figure 1: This BGA assembly is both the best and worse assembly ever. Worst because it has so many defects; best because it allows us to exemplify, in one image, most defects encountered in BGA assembly.
First up: opens. An open circuit, or “open,” occurs when the solder ball fails to collapse and doesn’t touch the pad on the board. Open solder joints on a BGA are an indication of insufficient solder paste, or that the component is not sufficiently coplanar. Opens can also be caused by contamination or an insufficiently clean board. It is another condition that is relatively easy to identify with X-ray inspection and again, if caught early, can usually be addressed with adjustment to your process.
Solder splatter has a few common causes:
- Moisture contamination of solder paste can cause rapid outgassing during reflow, resulting in splatter.
- Splatter can also be an indication that oven profiles are off.
- Excessive ramp rate during reflow is another common culprit causing solder splatter, as solvents in solder paste need to outgas gradually.
- Sometimes humidity is the culprit, as moisture in the solder paste can cause it to explode as the gases expand rapidly.
It’s essential to bring solder paste to room temperature prior to reflow to prevent moisture from condensing on the paste. Once again, early inspection during production can help inform adjustment that reduce rework and scrap.
Properly applied solder mask will prevent oxidation and protect against solder bridging. While it is essential, it can cause problems if it interferes with pads or is too thick. Diagnosing solder mask problems is, in part, a function of the board layout. Design options for BGA and solder mask include designing the mask on the pad—or not. If the solder pad is defined, the edges of the pad are covered with solder mask and proper solder mask adhesion and deposition must be verified. If the solder mask is not defined on the pad, the pad edges are exposed and alignment becomes critical. If the solder mask is not centered on the pad, the trace can be overexposed, thus causing solder run and potentially an open or short circuit.
Voids in the solder balls themselves are common in BGAs and are only problematic when voiding is excessive. Voids occur when entrapped flux from solder paste vaporizes rapidly and resulting gases rise within the molten solder. Due to buoyancy, voids are most often located near the package interface. Excessive voiding can cause individual balls to develop cracks (opens) over time. Void analysis with X-ray inspection allows for quantifying voiding and ensuring that the percent voiding of given components conforms to manufacturers requirements; typically, the higher reliability demanded, the lower the acceptable percent voiding. When caught early in a run, voiding can be reduced by adjustments to ramp and temperature of your reflow oven.
At the risk of seeming shallow, looks do matter, and solder ball shape is an important indicator of quality. The ideal shape of a solder ball is round. When seen through an X-ray image, there should be a uniform grid of dark circles. The primary cause if misshaped BGA balls is the alignment of the package to the board. If a solder ball does not land directly on top of the board, it can elongate (as a result of surface tension) to make the connection, resulting in an oval-shaped profile. Excessive solder deposition on the pad can also result in misshaped balls, as the excess solder combines with the BGA ball.
Missing balls are easy to identify, but their causes may not be immediately obvious. BGA balls can separate mechanically from the package during placement or in handling of the component. Metallurgical problems can also be a cause if they inhibit the solder’s ability to wet to the pad. Sometimes the problem is with the stencil used in printing the solder balls. A dirty stencil with a clogged opening may not deposit adequate solder on the pad to create a ball. Likewise, if solder paste is too thick, it may not flow properly through the stencil, clean or not.
As inspection techniques and equipment advance, BGA quality assurance becomes more automated. But it’s still important to understand and review these common BGA problems, be aware of the factors that contribute to them, and thus make them rare. Longer lasting, more reliable products, and happier customers will result, as will improved profits from avoiding costly rework and scrap. I hope this review has helped.
Dr. Bill Cardoso is CEO of Creative Electron.
More Columns from X-Rayted Files
X-Rayted Files: Best Practices in Buying MachinesX-Rayted Files: ’23 and Me?
X-Rayted Files: Battery-Powered Advancements Keep on Ticking
X-Rayted Files: What’s Cooler Than X-ray?
X-Rayted Files: My Favorite BGA Assembly Ever, Part 2
X-Rayted Files: My Favorite BGA Assembly Ever
X-Rayted Files: Smart vs. Intelligent SMT Factory
X-Rayted Files: X-ray Everything!