-
-
News
News Highlights
- Books
Featured Books
- smt007 Magazine
Latest Issues
Current IssueSpotlight on India
We invite you on a virtual tour of India’s thriving ecosystem, guided by the Global Electronics Association’s India office staff, who share their insights into the region’s growth and opportunities.
Supply Chain Strategies
A successful brand is built on strong customer relationships—anchored by a well-orchestrated supply chain at its core. This month, we look at how managing your supply chain directly influences customer perception.
What's Your Sweet Spot?
Are you in a niche that’s growing or shrinking? Is it time to reassess and refocus? We spotlight companies thriving by redefining or reinforcing their niche. What are their insights?
- Articles
- Columns
- Links
- Media kit
||| MENU - smt007 Magazine
Estimated reading time: 4 minutes
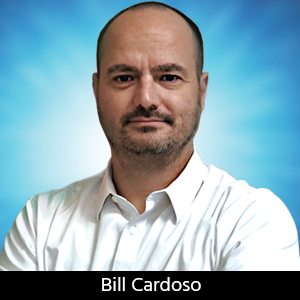
X-Rayted Files: A Century of X-Rays in the Automotive Industry, Part 2
In Part 1 of this column series, we explored the intimate relationship between the evolution of the X-ray and automotive industries. As one of the main users of X-ray inspection, the automotive industry has been one of the main drivers for the development of higher power and higher resolution X-ray imaging systems. Keep in mind that cars today are nothing but highly sophisticated computers. The simple analog dashboards with a speedometer and odometer have been replaced by complex entertainment centers.
While demands for ever-smaller electronics have dominated PCB design, and surface-mount components emerged in response to such demand, industries like automotive and aerospace still rely on through-hole components for their reliability in the harshest environments. The strength of the connection of surface-mount components is limited by their thin solder joints, and are thus less reliable under stresses such as vibration, shock, and high temperatures.
Through-hole components are mechanically stronger because their leads run through the board, and the solder joints are much more substantial and less susceptible to an array of environmental stresses. These properties make through-holes the ideal choice for larger components, as well as those with high-power demands, especially in extreme environments that involve rapid acceleration/deceleration, vibration, and thermal expansion/contraction.
Through-hole via (THV) solder filling plays an important role in the long-term reliability of through-hole components. The inadequate filling of THV can, over time, cause mechanical stresses that can result in traces connected to the THV to break. Insufficient THV filling also causes damage to the via itself, causing cracks and splits on the via. These effects are especially present in applications that subject boards to mechanical and thermal stresses, such as equipment in the military, automotive, and aerospace industries.
The diagnostic of THV filling must be done using an X-ray inspection system, preferably with an angled view. The need for an angled view X-ray inspection lies in the nature of the THV. A top view of the view will not produce an adequate perspective of how much solder the THV has.
Figure 1 shows the cross-section representation of an empty, partially filled, and completely filled THV. Due to capillarity, the solder wave flows from the solder source side to the component side. In so doing, it wets the connecting surface of the solder side, surrounds the pin, and forms a solder meniscus on account of the protrusion of the pin on the solder side.
Figure 2 shows the X-ray image of a similar assembly, where partially and completely filled vias are shown. This X-ray displays the importance of an angular inspection to determine the via solder fill in a THV assembly.
The yellow, green, and red lines in Figure 3 illustrate how the THV filling software measures the amount of solder inside the barrel or via. Figure 3 shows an X-ray image of empty, partially filled, and filled THV. The colored ovals in the figure match the color representation, shown in Figure 1, so that you can visualize the location of the solder inside the via. To measure via fill, the software determines the relative distances between the yellow-to-green and yellow-to-red makers to measure the percentage of via fill.
Other than solder penetration problems, IPC-A610E also accounts for issues related to the partial filling of the THV around the component lead. Table 1 summarizes the pass criteria for THV:
- Class 1, General Electronic Products: Includes products suitable for applications where the major requirement is function of the completed assembly.
- Class 2, Dedicated Service Electronic Products: Includes products where continued performance and extended life is required, and for which uninterrupted service is desired but not critical. Typically, the end-use environment would not cause failures.
- Class 3, High-Performance/Harsh Environment Electronic Products: Includes products where continued high performance or performance-on-demand is critical, equipment downtime cannot be tolerated, end-use environment may be uncommonly harsh, and the equipment must function when required, such as life support or other critical systems.
Figure 4 shows examples of how to use your X-ray inspection system to diagnose these problems. In this case, contrary to the X-ray images in Figure 2, the X-ray sensor was positioned right above the THV for a top-down view of the whole THV column.
When troubleshooting THV issues, here are some of the things you can take a look at to improve your process:
- Adequate solder quantity deposited
- Proper solder to guarantee wetting
- Proper surface cleaning of PCB to eliminate contamination that will block the proper flow of solder
- Inadequate temperature of solder so that it doesn’t complete the reflow process properly; it is important to consider the thermal mass of the component and the board (e.g., heavy copper planes require longer times or higher temperatures for proper solder flow)
- Inadequate time of the soldering process; it’s possible the components and THV are not reaching the right temperature (thus, the solder is not flowing up to the other end of the THV)
Dr. Bill Cardoso is CEO of Creative Electron.
More Columns from X-Rayted Files
X-Rayted Files: Best Practices in Buying MachinesX-Rayted Files: ’23 and Me?
X-Rayted Files: Battery-Powered Advancements Keep on Ticking
X-Rayted Files: What’s Cooler Than X-ray?
X-Rayted Files: My Favorite BGA Assembly Ever, Part 3
X-Rayted Files: My Favorite BGA Assembly Ever, Part 2
X-Rayted Files: My Favorite BGA Assembly Ever
X-Rayted Files: Smart vs. Intelligent SMT Factory